無(wú)鉛制造中的測(cè)試與檢測(cè)
圖1是HP Loveland工廠在多條生產(chǎn)線上使用免清洗無(wú)鉛工藝生產(chǎn)產(chǎn)品的焊接缺陷統(tǒng)計(jì)圖,產(chǎn)品線路板為中/低組裝密度,器件種類較多,因?yàn)槭窃诙鄺l生產(chǎn)線上完成的多品種產(chǎn)品,因此從器件到焊接材料,都存在著一個(gè)較大的變動(dòng)范圍。剛開(kāi)始采用無(wú)鉛焊料時(shí),缺陷的PPM值很高,經(jīng)過(guò)大約2年時(shí)間的工藝改進(jìn),缺陷的PPM值降到了原來(lái)使用SnPb焊料時(shí)缺陷程度的2倍左右。從錫鉛向無(wú)鉛的轉(zhuǎn)換過(guò)程中,以下幾個(gè)問(wèn)題對(duì)測(cè)試/檢測(cè)控制是非常重要的:
多數(shù)情況下焊接缺陷率升高
從焊膏印刷、貼片、爐前、爐后、波峰焊后、ICT,功能測(cè)試不同階段分別進(jìn)行焊接缺陷統(tǒng)計(jì)分析
工藝問(wèn)題增多,對(duì)工藝控制(SPI,AOI)等要給予更高的重視,最終產(chǎn)品高缺陷率對(duì)生產(chǎn)工藝,測(cè)試/檢測(cè)方法也提出新的要求
為減少維修的麻煩,高診斷能力的測(cè)試/檢測(cè)方法十分重要

潤(rùn)濕特性不同
影響焊點(diǎn)形狀的因素有:熔融焊料的潤(rùn)濕性及表面張力,焊盤與引腳鍍層的材料,以及無(wú)鉛焊料的潤(rùn)濕性沒(méi)有錫鉛焊料強(qiáng)。
以上幾點(diǎn)對(duì)無(wú)鉛產(chǎn)品焊點(diǎn)的形狀及缺陷率產(chǎn)生了直接的影響。焊接缺陷增多的主要原因是無(wú)鉛焊料的潤(rùn)濕性差,請(qǐng)看下面幾個(gè)與焊料潤(rùn)濕特性相關(guān)的實(shí)例:
1、焊盤覆蓋率。因?yàn)闊o(wú)鉛焊料潤(rùn)濕性降低,回流后留在焊盤上的焊料不能完全覆蓋焊盤。如圖2所示,這只是兩個(gè)空焊盤上錫鉛焊料與無(wú)鉛焊料的比較,左圖為傳統(tǒng)的錫鉛焊料形成的焊點(diǎn),很明顯其焊料回流后全部覆蓋焊盤;而右圖的無(wú)鉛焊料經(jīng)回流后形成的焊點(diǎn)只覆蓋右半部焊盤。在PCB無(wú)鉛裝配過(guò)程中,像右圖的焊點(diǎn)情況通常視為合格,但這樣的焊點(diǎn)對(duì)傳統(tǒng)的在線測(cè)試(ICT)及功能測(cè)試結(jié)果會(huì)產(chǎn)生一定的影響。如果這是一個(gè)測(cè)試焊盤,探針就有可能損害到焊料未完全覆蓋的裸露的焊盤部分。根據(jù)以往的測(cè)試經(jīng)驗(yàn),裸露焊盤部分只有助焊劑殘留物覆蓋,探針容易刺傷焊盤而不能形成良好接觸,造成ICT及功能測(cè)試通過(guò)率降低。
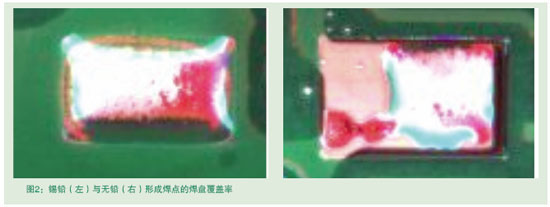
2、另一個(gè)潛在的問(wèn)題是彎曲變形的引腳。對(duì)于引腳稍有彎曲變形的器件,其在錫鉛焊接過(guò)程中因焊料的潤(rùn)濕力較大,一般情況下回流后能獲得合格焊點(diǎn);而同樣的器件在使用無(wú)鉛焊料時(shí),多數(shù)情況下產(chǎn)生開(kāi)路或焊點(diǎn)可靠性降低,而不能形成合格的焊點(diǎn)。
3、潤(rùn)濕力對(duì)偏移器件的影響。如果器件貼裝時(shí)偏位,使用錫鉛焊料在回流過(guò)程中產(chǎn)生自對(duì)中能力,可以把貼裝偏位的器件拉回到焊盤上,形成良好焊點(diǎn);同樣對(duì)無(wú)鉛焊料講,由于潤(rùn)濕力的降低,焊料回流過(guò)程中,不能將器件拉回到焊盤上,而焊料只是在原位熔融、固化,因此,要想在無(wú)鉛焊接中得到良好的焊點(diǎn),就必須提高貼片機(jī)的貼裝精度或爐前進(jìn)行人工校正,不然回流后偏移這一缺陷會(huì)顯著增加。
4、潤(rùn)濕力還影響到相鄰焊盤間的橋接/短路。錫鉛焊料的潤(rùn)濕力通??蓪⒑噶夏鄣胶副P上,消除橋接產(chǎn)生的機(jī)會(huì);而無(wú)鉛焊料因?yàn)闈?rùn)濕力差,相鄰焊盤間焊料熔融后不能全部拉回到焊盤上,在相鄰焊盤之間殘留的焊料形成橋接,造成短路。
5、潤(rùn)濕力對(duì)波峰焊接的影響。在波峰焊接過(guò)程中,熔融的焊料填充到通孔中,形成焊點(diǎn)。錫鉛焊料波峰焊接時(shí),焊料填充滿通孔,形成的焊點(diǎn)牢固可靠;無(wú)鉛焊料用于波峰焊接時(shí),熔融的焊料因潤(rùn)濕力差,不能填滿通孔。圖3是通過(guò)X光檢測(cè)到的無(wú)鉛焊料的波峰焊后情況,只有部分無(wú)鉛焊料附著在了通孔壁上。
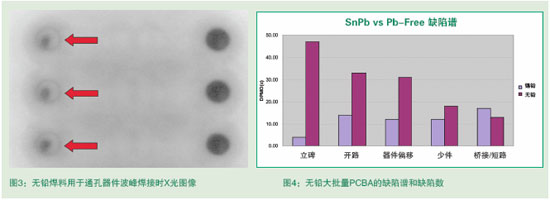
目前,使用無(wú)鉛焊料帶來(lái)問(wèn)題的例子有很多,其中大多數(shù)經(jīng)驗(yàn)來(lái)自大批量消費(fèi)類電子產(chǎn)品制造領(lǐng)域。因?yàn)榇蠖鄶?shù)消費(fèi)類電子產(chǎn)品的板型簡(jiǎn)單,器件/焊點(diǎn)數(shù)量不大,器件類型的變化也不快。下面是對(duì)二種相似板型的同一種CM產(chǎn)品進(jìn)行的試驗(yàn):其中一種采用錫鉛焊料,另一種采用無(wú)鉛焊料,二種板子都是消費(fèi)類電子產(chǎn)品,最小的是0.5mm間距的器件(BGA,翼型引腳元器件,SMT連接器),板上最小的片式元件為0402(英制)。每塊板上大約有1300個(gè)元器件,焊點(diǎn)數(shù)大約為3,000個(gè)。使用錫鉛焊料的板子批量為85,000PCS,使用無(wú)鉛焊料的板子批量為60,000PCS,圖4是記錄的二種板子的缺陷譜和缺陷數(shù)(注意,圖中所示的只是對(duì)無(wú)鉛工藝有重要影響的缺陷種
類)。
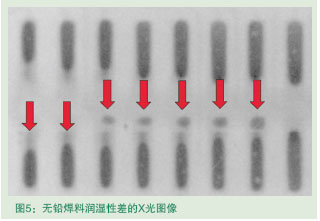
從圖中可以看出,立碑現(xiàn)象變化最大,主要發(fā)生在0402元件上,開(kāi)路、移位現(xiàn)象在錫鉛焊接上也有發(fā)生,無(wú)鉛焊接中只有橋接/短路發(fā)生率下降,好像與我們預(yù)料的不同。也許是無(wú)鉛焊接過(guò)程控制嚴(yán)格的緣故吧,因?yàn)楣こ處煂?duì)無(wú)鉛生產(chǎn)設(shè)備,工藝都做了適當(dāng)?shù)恼{(diào)整。DPMO統(tǒng)計(jì)結(jié)果:無(wú)鉛焊接缺陷率
•空洞:空洞產(chǎn)生幾率顯著增加,空洞對(duì)產(chǎn)品的影響尚需進(jìn)一步研究
•立碑:立碑現(xiàn)象顯著增加
焊料不足:波峰焊接過(guò)程中,通孔中焊料明顯減少•橋接:主要存在于波峰焊,選擇性波峰焊中
錫須:對(duì)長(zhǎng)期可靠性有影響,不幸的是,現(xiàn)在已有產(chǎn)品在測(cè)試中出現(xiàn)問(wèn)題
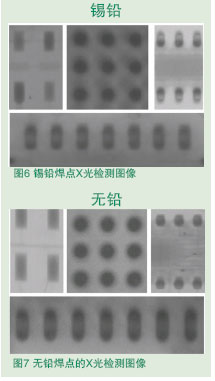
無(wú)鉛測(cè)試策略
1、實(shí)施無(wú)鉛焊接之前對(duì)正在進(jìn)行的錫鉛焊接工藝建立一套完整的工藝體系。當(dāng)確定了正常的缺陷水平和缺陷譜,從測(cè)試/檢測(cè)角度找到瓶頸在哪里,并對(duì)無(wú)鉛焊接可能產(chǎn)生的缺陷有了正確的預(yù)測(cè)之后,方可實(shí)施無(wú)鉛導(dǎo)入。
2、對(duì)于有多條生產(chǎn)線的加工企業(yè),應(yīng)從一條生產(chǎn)線開(kāi)始轉(zhuǎn)入無(wú)鉛焊接,并在該條生產(chǎn)線上嚴(yán)格執(zhí)行測(cè)試/檢測(cè),充分利用分析軟件進(jìn)行分析。正如前面提到過(guò)的,向無(wú)鉛轉(zhuǎn)換的過(guò)程中,會(huì)有很多問(wèn)題出現(xiàn):要解決潤(rùn)濕性問(wèn)題回流溫度和波峰焊接溫度的升高后器件的耐熱問(wèn)題工藝窗口變小的情況下回流曲線的建立問(wèn)題等。一套好的工藝程序應(yīng)從絲網(wǎng)印刷開(kāi)始,加強(qiáng)印刷后焊膏檢測(cè),回流過(guò)程中注意預(yù)熱控制;一條好的回流曲線可降低焊接缺陷,收集各工藝段的測(cè)試/檢測(cè)數(shù)據(jù),并加以分析,有助于提高生產(chǎn)工藝能力,降低焊接缺陷,可按缺陷增加類型調(diào)整檢驗(yàn)標(biāo)準(zhǔn)。當(dāng)所有問(wèn)題得到解決,缺陷率及質(zhì)量合格率可接受后,方可開(kāi)始進(jìn)行其他生產(chǎn)線向無(wú)鉛工藝的轉(zhuǎn)換。
3、注意,當(dāng)同一條生產(chǎn)線從一種板型轉(zhuǎn)換為另一種板型時(shí),也會(huì)有較大的工藝變化,也許某些板型轉(zhuǎn)換過(guò)程中會(huì)有少量問(wèn)題出現(xiàn),而其它板型的焊接缺陷會(huì)急劇升高,出現(xiàn)較多的問(wèn)題。因此,用一條生產(chǎn)線作為向無(wú)鉛轉(zhuǎn)換的測(cè)試線,解決出現(xiàn)的問(wèn)題,分析潛在的問(wèn)題,解決產(chǎn)生不良影響的工藝問(wèn)題,從而使所有生產(chǎn)線順利轉(zhuǎn)到無(wú)鉛化生產(chǎn)。
無(wú)鉛對(duì)測(cè)試/檢測(cè)方法與設(shè)備的要求
焊膏檢測(cè)(SPI)
更換為無(wú)鉛焊膏后,印刷工藝也要做適當(dāng)?shù)恼{(diào)整,使用3DSPI可快速優(yōu)化印刷參數(shù),改善印刷性能。通過(guò)過(guò)去10年以上的錫鉛印刷工藝參數(shù)的研究,焊膏印刷體積與焊點(diǎn)長(zhǎng)期可靠性之間有著密切的關(guān)系。無(wú)鉛焊膏的印刷量對(duì)無(wú)鉛焊點(diǎn)的可靠性及其它相關(guān)問(wèn)題有著同樣的影響,因此,對(duì)3DSPI的需求更為迫切。對(duì)稱焊盤上印刷同樣體積的焊膏可以減少立碑的產(chǎn)生,使用3DSPI檢測(cè)系統(tǒng)可以在焊接前預(yù)測(cè)潛在問(wèn)題,對(duì)后面的回流工藝有一定的幫助,可減少實(shí)際應(yīng)用中的缺陷產(chǎn)生,是向無(wú)鉛轉(zhuǎn)換中的一個(gè)重要的控制手段。
爐前,爐后AOI檢測(cè)
應(yīng)用AOI對(duì)焊點(diǎn)進(jìn)行檢測(cè)時(shí),無(wú)鉛與錫鉛焊點(diǎn)的顏色稍有不同,無(wú)鉛焊膏的潤(rùn)濕性比錫鉛焊膏差,AOI檢測(cè)到的無(wú)鉛焊點(diǎn)顏色較淺,為此英國(guó)國(guó)家物理研究實(shí)驗(yàn)室(NPL)對(duì)六家供應(yīng)商提供的AOI設(shè)備進(jìn)行了測(cè)評(píng),結(jié)果在2002年6月公布。研究表明,現(xiàn)有的AOI檢測(cè)系統(tǒng)測(cè)試出的無(wú)鉛與錫鉛焊接結(jié)果稍有不同,但不影響對(duì)焊點(diǎn)好壞的判別,完全有能力對(duì)無(wú)鉛PCB焊點(diǎn)進(jìn)行檢測(cè)。因此,現(xiàn)在大多數(shù)AOI檢測(cè)設(shè)備可用于無(wú)鉛檢測(cè)。
AXI(自動(dòng)X光檢測(cè))
X光檢測(cè)可以直接觀察焊點(diǎn)圖像,能否用于無(wú)鉛焊接?回答是肯定的。無(wú)鉛焊點(diǎn)產(chǎn)生的圖像有足夠的對(duì)比度來(lái)觀察焊點(diǎn)情況,圖6是使用傳統(tǒng)的錫鉛焊料的X光圖像,圖7是使用無(wú)鉛焊料的X光圖像。從兩個(gè)圖像中可以看出,錫鉛與無(wú)鉛的X光圖像無(wú)太大差別,由于人類視覺(jué)對(duì)灰度的辨別能力,觀察出的無(wú)鉛焊點(diǎn)比錫鉛焊點(diǎn)薄1520%,精確測(cè)量時(shí)可以增加這一補(bǔ)償,實(shí)際觀察到的焊點(diǎn)形狀是基本相同的,因此,X光可以應(yīng)用于無(wú)鉛焊接的產(chǎn)品檢測(cè)上。
ICT
ICT測(cè)試基礎(chǔ)是探針與焊盤(點(diǎn))之間有良好的接觸,成功檢測(cè)的原理是使用硬的尖利的探針刺穿測(cè)試點(diǎn)上的助焊劑殘留物及其它氧化物,與測(cè)試點(diǎn)上覆蓋的焊料有良好的接觸,刺穿深度由探針的材料及形狀決定;刺得越深,與測(cè)試點(diǎn)的接觸越好。
錫鉛焊點(diǎn)的硬度大約為5000PSI,與之匹配的探針是80Z不銹鋼或鍍鈹探頭的探針,以上匹配可以達(dá)成良好接觸。熱風(fēng)整平的PCB在測(cè)試點(diǎn)上已形成錫鉛焊點(diǎn),與探針容易形成良好接觸。而適用于無(wú)鉛的OSP處理的PCB表面,需要通過(guò)模板印刷,回流后形成與探針接觸的測(cè)試點(diǎn),測(cè)試點(diǎn)上焊料的多少是由模板決定的。
一般情況下,PCB文件中不包括測(cè)試點(diǎn),在模板制作時(shí)要考慮到測(cè)試點(diǎn)的位置,否則測(cè)試點(diǎn)上沒(méi)有焊料而成為裸銅焊盤。裸銅的伸展強(qiáng)度高,電遷移較鉛基焊料嚴(yán)重,又因裸銅焊盤較薄,容易被探針刺傷。此外,OSP處理過(guò)的PCB回流后,裸銅焊盤極易氧化,造成探針與測(cè)試點(diǎn)之間接觸性差,影響ICT測(cè)試。
因此,在無(wú)鉛產(chǎn)品測(cè)試時(shí),切記不可使用裸銅焊盤的測(cè)試點(diǎn),制作模板時(shí)要考慮測(cè)試點(diǎn)上的焊膏印刷。對(duì)于OSPPCB,制作模板時(shí)要考慮測(cè)試點(diǎn)開(kāi)孔,回流過(guò)程中,熔融焊料覆蓋焊盤,令測(cè)試點(diǎn)與探針之間形成良好接觸。
無(wú)鉛焊料的延伸強(qiáng)度比大多數(shù)鉛基焊料形成的焊點(diǎn)強(qiáng)度小,接觸點(diǎn)會(huì)稍小一些,測(cè)試點(diǎn)上錫的氧化物是導(dǎo)體,不影響探針與測(cè)試點(diǎn)的接觸,相對(duì)于錫鉛焊料時(shí)探針必須刺穿氧化層要省力。
由于無(wú)鉛焊料可焊性較差,必須選用活性強(qiáng)的助焊劑來(lái)提高潤(rùn)濕性,因此無(wú)鉛焊料形成的助焊劑殘留物比使用錫鉛焊料要多且硬,很難被探針刺穿。當(dāng)出現(xiàn)問(wèn)題時(shí),可與供應(yīng)商聯(lián)系以減少助焊劑帶來(lái)的麻煩。
功能測(cè)試
無(wú)鉛焊接主要是焊料要求回流溫度升高,這樣會(huì)增加返修對(duì)PCBA造成的潛在危害以及增加高密度PCBA的返修難度。最好的解決方法是通過(guò)功能檢測(cè)校正前道生產(chǎn)工藝,降低過(guò)程缺陷。此外,在功能測(cè)試發(fā)現(xiàn)短路時(shí),通常使用熱風(fēng)槍處理,否則只能更換器件。根據(jù)測(cè)試結(jié)果診斷分析,利用先進(jìn)的軟件功能修改測(cè)試程序,消除潛在問(wèn)題,可節(jié)約返修資金。
PCBA功能測(cè)試是通過(guò)板子四周(邊緣)的連接器或板針來(lái)完成的,板針測(cè)試時(shí)也有ICT測(cè)試時(shí)接觸方面的問(wèn)題,建議采用上述ICT處理方法。
評(píng)論