高側(cè)電流檢測的測量:集成電路和原則-High-Side
Current measurement (monitoring current flow into and out of electronic circuits) is an essential skill in the designer's repertoire and necessary in a wide range of applications. Examples include overcurrent-protection and supervising devices, 4-20mA systems, programmable current sources, linear and switch-mode power supplies, battery chargers, and battery-operated circuits for which you must know the ratio of current flow into and out of a rechargeable battery (that is, the gauge function).
As more applications become portable, the demand increases for dedicated current monitors that accomplish their task in a small package and with low quiescent current. The following discussion covers low-side and high-side current monitors and includes their architectures and applications.
High- or Low-Side Monitor?
Most current-measurement applications employ either the low-side principle, in which the sense resistor connects in series with the ground path (Figure 1), or the high-side principle, in which it connects in series with the hot wire (Figure 2). These two approaches pose a trade-off in different areas: The low-side resistor adds undesirable extraneous resistance in the ground path, and circuitry associated with the high-side resistor must cope with relatively large common-mode signals. Moreover, if the op amp in Figure 1 has its GND pin referred to the positive side of RSENSE, then its common-mode input range must extend below zero, that is, to GND -(RSENSE x ILOAD).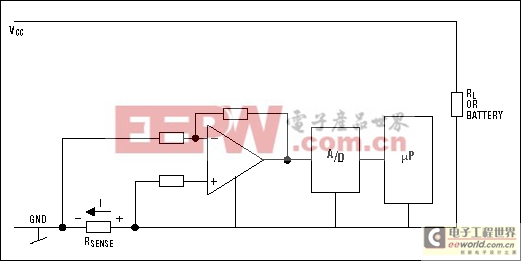
Figure 1. Principle of the low-side current monitor.
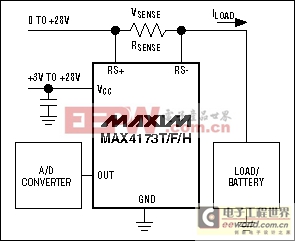
Figure 2. Example of a high-side current monitor.
However, don't let the simplicity of a low-side measuring circuit cause you to overlook the advantages of a high-side approach. Various faults can bypass the low-side monitor, thereby subjecting the load to dangerous and undetected stress (Figure 3). Note that loads connected through path A are monitored, but an accidental connection though path B bypasses the monitor. A high-side monitor connected directly to the power source, on the other hand, can detect any downstream failure and trigger appropriate corrective action. High-side monitors are also well suited for automotive applications in which the chassis serves as the ground potential.
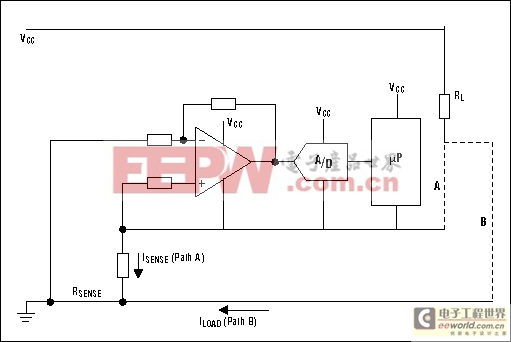
Figure 3. Path B can carry dangerously high currents if the load is connected accidentally to ground.
Traditional High-Side Monitor
Until recently, the many implementations of these two approaches were based on discrete components or semidiscrete circuitry. In their simplest form, such high-side monitors require a precision op amp and a handful of precision resistors. One common approach for high-side measurements has been the use of the classic differential amplifier, which is employed as a gain amplifier and a level shifter from the high side to ground (Figure 4). Though widely used, this discrete circuit has three major disadvantages:- Input resistance (equal to R1) is relative low.
- Inputs usually exhibit a large difference in input resistance.
- Resistors must be very well matched to obtain an acceptable common-mode rejection ratio (CMRR): A 0.01% deviation in any resistor value lowers the CMRR to 86dB, a 0.1% deviation lowers it to 66dB, and a 1% deviation lowers it to 46dB.
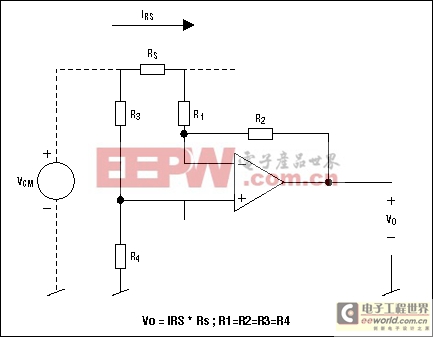
Figure 4. The differential amplifier is a basic component in high-side current measurements.
Integrated Differential Amplifier
The use of differential amplifiers in high-side current measurement recently became more convenient thanks to the introduction of numerous ICs containing not only the precision amplifier but well-matched resistors as well. These devices offer CMRRs on the order of 105dB. An example is the MAX4198/MAX4199 (Figure 5). Available in 8-pin μMAX packages, these ICs achieve a typical CMRR of 110dB and gain error better than 0.01%.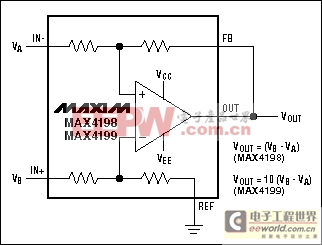
Figure 5. An integrated differential amplifier (MAX4198/MAX4199) exhibits very high CMRR.
Dedicated High-Side Monitors
Another approach to high-side current measurement is represented by ICs that contain all functions necessary to perform the measurement. They sense high-side currents in the presence of common-mode voltages as high as 32V and provide a ground-referenced current- or voltage-source output that is proportional to the current of interest. Power management, battery charging, and other applications that must accurately measure or control current can benefit from these dedicated current-sense amplifiers.High-side current-sense amplifiers from Maxim employ a current-sensing resistor placed between the positive terminal of the power supply and the supply input of the monitored circuit. This arrangement avoids extraneous resistance in the ground plane, greatly simplifies the layout, and generally improves the overall circuit performance. The variety of uni- and bidirectional current-sense ICs from Maxim includes bidirectional devices with or without internal sense resistors. The bidirectional amplifiers comprise a sign pin for indicating current direction.
These uni- and bidirectional current-sense ICs include models with adjustable gain, fixed internal gains of +20V/V, +50V/V, or +100V/V, and internal gain plus a single or dual comparator. They come in small packages to meet the strict demands of compact applications. (Maxim has the only high-side current-sense amplifier in a tiny SOT23 package.)
Common to all high-side IC monitors from Maxim is an ability to provide ground-referenced voltage or current outputs with few or no additional components. The output signal is proportional to the measured high-side current, which can have a common-mode voltage as high as 32V. Figures 6 through 9 show some available architectures for the integrated high-side current monitor. Note that the MAX471/MAX472 current-source output is proportional to the voltage across RSENSE.
Equations for the new high-side monitors indicate that the effect of external resistors on the CMRR is no longer an issue, because CMRR (typically >90dB) is now determined by the integrated amplifier alone. Integration of the current-measure function in a single IC provides the following advantages:
- Tight tolerance on active and passive integrated components
- An excellent temperature coefficient (TC)
- Small size
- Low power consumption
- Ease of use
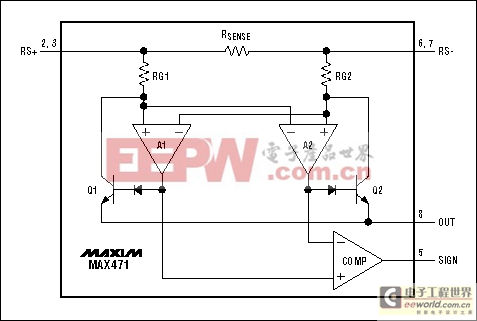
Figure 6. This simplified schematic of a bidirectional high-side current monitor (MAX471/MAX472) includes a SIGN output for current direction.
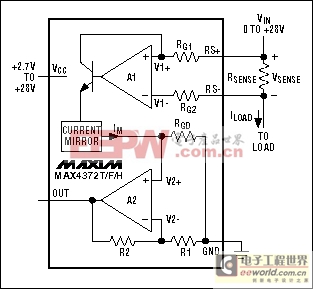
Figure 7. A unidirectional high-side current monitor (MAX4372).
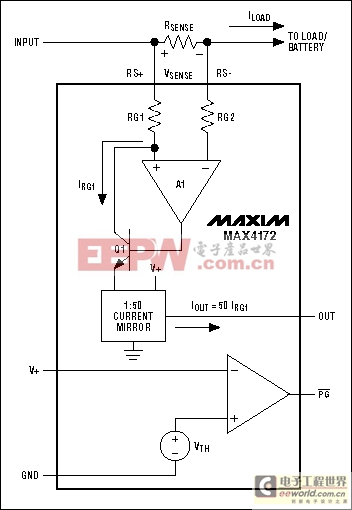
Figure 8. Another unidirectional high-side current monitor (MAX4172).
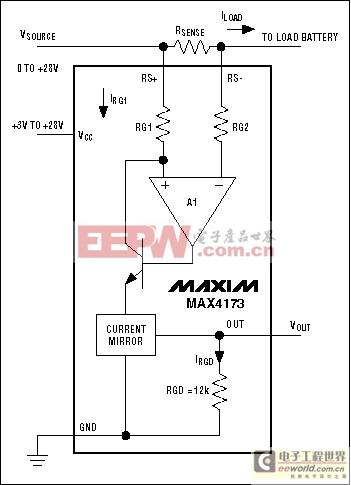
Figure 9. Yet another architecture for the unidirectional high-side current monitor (MAX4173).
Considerations When Selecting RSENSE
A careful consideration of the shunt resistor (RSENSE) is an important and necessary part of designing any kind of current monitor. The following criteria should govern the selection of RSENSE:- Voltage Loss: High RSENSE values cause the power-source voltage to degrade through IR loss. The lowest RSENSE value gives the least voltage loss.
- Accuracy: High RSENSE values let you measure low-level currents more accurately, because the voltage offset and input bias-current offsets are less significant with respect to the sense voltage.
- Efficiency and Power Dissipation: At high current levels, the I2R loss in RSENSE can be substantial, so take that into consideration when choosing the resistor value and power-dissipation rating (wattage). Excessive heat in the sense resistor can also cause its value to drift.
- Inductance: If ISENSE has a large high-frequency component, RSENSE must have low inductance. Wire-wound resistors have the highest inductance. Metal-film resistors are somewhat better, but low-inductance metal-film resistors (available in values under 1 1/2 Ω) are recommended. Unlike the metal-film and wire-wound types (spiral-wrapped around a core), low-inductance metal-film resistors consist of a straight band of metal.
- Cost: Using a PC-board trace as a sense resistor (Figure 10) is an alternative method for applications where the cost of RSENSE is an issue. You will need to adjust the full-scale current value with a potentiometer because of inaccuracy in the copper resistance. The resistance temperature coefficient of copper is fairly high (approximately 0.4%/°C) in systems that undergo wide temperature variations.
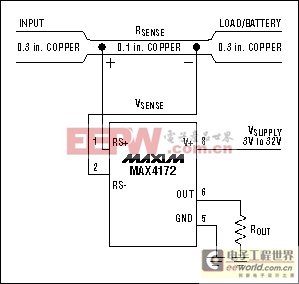
Figure 10. This high-side current monitor (MAX4172) employs a PC-board trace for RSENSE.
High-Side-Monitor Applications
The circuit in Figure 11 is a variable linear current source. IC1 converts R1 current to a proportional output voltage, enabling the voltage regulator (IC2) to produce a regulated output current. To set a specific, regulated IOUT level between 0mA and 500mA, apply 5V to 0V at ICONTROL (5V sets IOUT = 0mA, and 0V sets IOUT = 500mA). As an alternative, you can introduce a D/A converter as shown to provide digital control of IOUT. For 12-bit resolution (60μA per LSB), the DAC can be a parallel-input MAX530 or serial-input MAX531. For 10-bit resolution (250μA per LSB), the DAC can be a parallel-input MAX503 or a serial-input MAX504.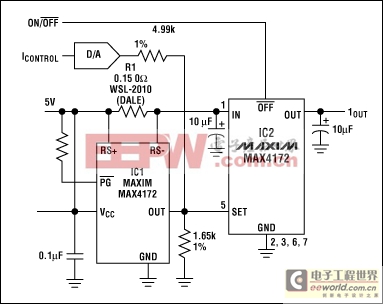
Figure 11. A variable, linear current source (MAX4173).
The Figure 12 circuit is a 0-5A programmable variable current source. Generating 0A to 5A with a compliance range of 4V to 28V, it offers two advantages: The 12-bit D/A converter (IC2) makes it digitally programmable, and the switch-mode step-down regulator (IC1) makes it more efficient than the alternative current source with the linear pass transistor. Applications include battery charging and DC motor control.
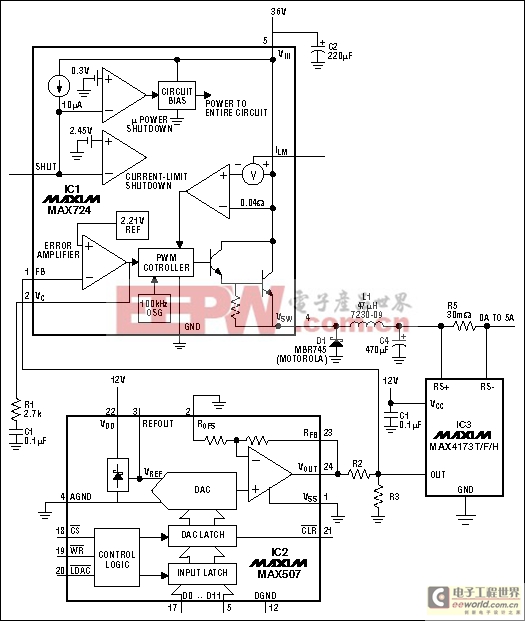
Figure 12. A 0-5A programmable current source (MAX4173).
Widespread use of the universal serial bus (USB) has led to a variety of overcurrent protection circuits for supply rails in the range +2.7V to +5.5V, but few products are available for voltages above that range. The circuit breaker in Figure 13 operates on supply voltages to +26V and trips at a programmed current threshold.
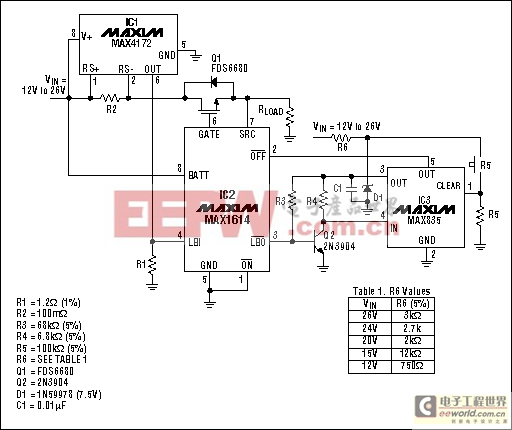
Figure 13. This high-voltage circuit breaker (MAX4172) protects to 26V.
pic相關(guān)文章:pic是什么
電流傳感器相關(guān)文章:電流傳感器原理
評論