隔離式電源電信應(yīng)用-Isolated Power Suppl
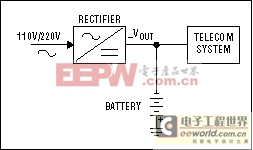
Figure 1. In this block diagram of the backup architecture used in telecom systems, a battery block is kept charged by the mains rectifier. In the event of a mains failure, it supplies the system to prevent transmission interruptions.
ISDN and other systems powered by a remote source often operate with a higher input voltage: up to 120VDC. (Losses due to line resistance are proportional to the square of supply current, so the lower supply current associated with higher input voltage allows a longer transmission line.) By powering the telecom phone through the cable as well as the local mains, such systems eliminate the need for a backup battery at the cable's user end. When required, the cable therefore carries both transmission signals and supply current (Figure 2).
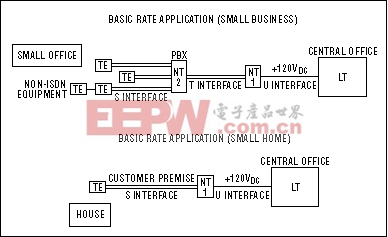
Figure 2. In an ISDN system for small-office or home applications, the phone lines normally carry forward transmissions. During emergencies, they carry power from the central office to the remote unit's network termination (NT) and terminal equipment (TE).
The selection of power-conversion topology depends on the level of output power required: forward or flyback for low power, push-pull for medium power, and half or full bridge for high power. The simplest configuration (flyback) stores energy in the transformer during the ON period of the primary PWM (when the power MOSFET is ON), and it releases it to the load during the OFF period (Figure 3). Because the secondary diode (D1) is forward-biased at that time, energy stored in the transformer goes to the load and charges the output capacitor. Energy stored in the output capacitor is delivered to the load during the next ON period. For this configuration, the primary-controller IC can have a fixed-frequency PWM configuration such as the MAX668 or a variable-frequency PFM configuration such as the MAX1771. A controller like the MAX5003 can be powered directly from the high input voltage.
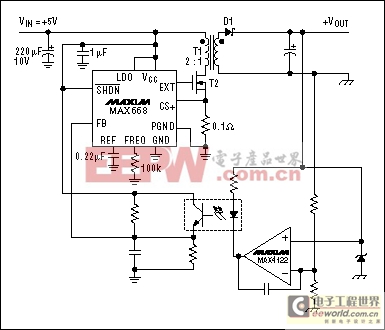
Figure 3. A flyback converter stores energy during every cycle: in the transformer when the power MOSFET is ON and forward to the load when the power MOSFET is OFF.
In the forward topology (Figure 4), energy is forwarded to the secondary when the primary's power MOSFET turns ON. Energy is not stored in the transformer as in a flyback circuit, so the forward configuration allows a smaller transformer and more power output. An output inductor on the secondary side stores energy and also reduces ripple current in the output capacitor. During an ON period, the load receives energy directly from the transformer trough diode D1 and L1; however, during an OFF period, inductor L1 forces diode D2 to conduct. Thus, L1 and C1 together maintain a continuous delivery of energy to the load.
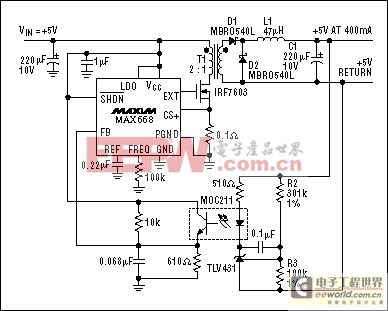
Figure 4. Because forward converters forward energy to the secondary side during every cycle, they don't require a large isolation transformer for storing energy.
The push-pull configuration (Figure 5) can be simplified as a double-forward converter in which the primary's two power MOSFETs alternate on and off. Energy-conversion principles for the push-pull and forward types are exactly the same during each half cycle, but push-pull circuits reset the transformer during each primary-to-secondary energy transfer (rather than during an OFF period). This action allows more output power for a given transformer geometry.
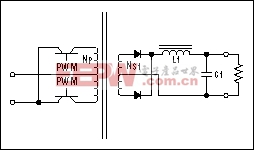
Figure 5. Push-pull converter.
Full-bridge configurations are generally used for power outputs over 1kW (Figure 6). They allow use of the transformer in two quadrants of the BH magnetization characteristic, rather than one as in the forward and flyback circuits (Figure 7). Also, the input-voltage swing seen by the transformer primary equals 2VIN rather than 1VIN. As the power MOSFET pair Q1/Q4 turns on together, then Q2/Q3, the transformer primary winding sees +VIN during the first cycle and -VIN during the second. Energy transfers to the load during each cycle of the secondary (as for the forward topology), but the better transformer optimization allows higher output power.
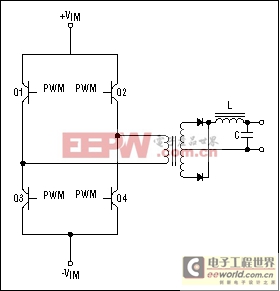
Figure 6. Full-bridge converter.
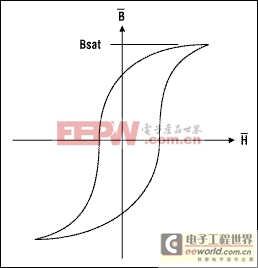
Figure 7. B-H magnetization shape of a magnetic material.
Yet other topologies are available. Resonant or quasi-resonant converters, for example (based on a resonant circuit inserted in the energy-conversion chain), reduce switching-power loss in the active element by avoiding square-wave signals of current and voltage. Whatever the topology, however, points common to all must be taken into consideration:
- EMI/RFI
- Safety
- Transient-voltage protection
- Output overcurrent and overvoltage protection
- Operating temperature and thermal protection
- Feedback
EMI/RFI
High-frequency operation (to 1MHz and higher) of the transformers in today's switching power supplies allows a reduction in all dimensions of those magnetic components. On the other hand, the high-frequency square waves (PWM or PFM topologies) or sine waves (resonant or quasi-resonant topologies) produce electromagnetic emissions during every cycle of energy transfer. International standards define limits for these emissions, which are conducted by the input and the output cables as EMI and radiated from space around the power supply as RFI.The international specification for conducted EMI and radiated RFI is EN55022, which lists maximum allowable amplitudes for EMI in the range 150kHz to 30MHz (Table 1) and for RFI in the range 30MHz to 1000MHz (Table 2). EN55022 also defines the tests needed for verifying compliance with its requirements, and it delineates the conditions necessary for approval of the laboratory in which the tests are conducted. Products that fail to meet these specifications for electromagnetic compatibility cannot be branded with the CE mark for sale in the European community or with UL approval for sale in the United States.
To meet specified limits for EMI and RFI, you must consider certain points during the design. First, identify sources of noise and minimize them as much as possible. In the 100kHz flyback topology in Figure 3, for example, five noise sources are easily identified:
1. Rise and fall time at the power MOSFET T1: According to Fourier analysis, this square wave can be regarded as a sum of harmonics: the first at 100kHz, the second at 200kHz, the third at 300kHz, etc., all with progressively lower amplitudes. Reducing the switching waveform's dV/dT minimizes the high-frequency harmonics, but a limit is imposed by the power dissipated during turn-on and turn-off.
2. T1 turn-off: During T1's turn-off, parasitic inductance and capacitance in the circuit and the transformer cause higher-frequency ringing in the drain voltage. This ringing energy can be minimized by specifying a transformer with small leakage inductance and by adding a diode/resistor/capacitor snubber circuit.
3. Ringing in D1: Similarly, an undesired noise frequency (ringing) due to parasitic capacitance in the secondary diode D1 can be reduced by a resistor/capacitor network in parallel with the diode.
4. RFI from the transformer: RFI noise caused by the flyback transformer's air gap can be reduced several decibels by shielding the transformer with copper foil.
5. Layout: All components carrying the switching waveform should be as small as possible, with short connections. A long connection can act as an antenna, transmitting unwanted noise almost everywhere.
In 99% of all cases, you can reduce the problem (but not solve it completely) by taking all these principles into account. They entail the cost of extra parts. Noise coming from the power supply and present at the battery input, for example, must be attenuated with an EMI filter that consis
評(píng)論