基于PLC的精煉爐自動控制系統(tǒng)研究
4 架構(gòu)設(shè)計
RH控制系統(tǒng)采用兩級控制系統(tǒng)組成,分別為一級基礎(chǔ)自動化系統(tǒng)和二級過程計算機控制系統(tǒng),兩級系統(tǒng)分別承擔不同的功能:
一、基礎(chǔ)自動化系統(tǒng)(L1級):管理整個RH生產(chǎn)過程,由PLC(包括分布各操作臺的遠程I/O)、OMS(人機接口)、工程師站、編程站及工業(yè)以太網(wǎng)絡(luò)組成。采集現(xiàn)場信號,完成電氣設(shè)備的邏輯順序控制、過程回路控制、設(shè)備運轉(zhuǎn)操作、設(shè)備監(jiān)視和報警等基本功能。
二、過程計算機控制系統(tǒng)(L2級):是以L1系統(tǒng)為基礎(chǔ)的相對獨立的系統(tǒng)。對整個RH系統(tǒng)生產(chǎn)過程進行管理和過程優(yōu)化,并為煉鋼廠更高級的管理信息系統(tǒng)及攀鋼ERP系統(tǒng)的建立留接口??刂葡到y(tǒng)結(jié)構(gòu)參見下圖:
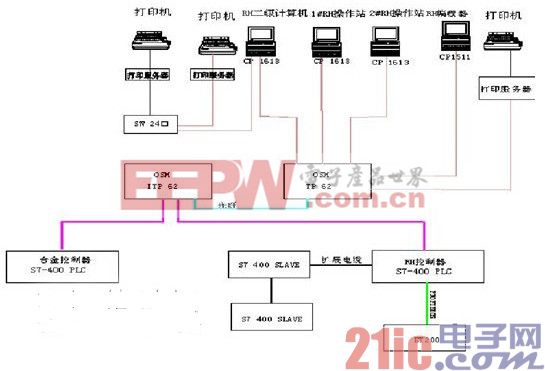
圖3 控制系統(tǒng)結(jié)構(gòu)
RH系統(tǒng)的控制分為兩部分,基礎(chǔ)自動化控制(L1)和過程計算機控制(L2)。一級控制主要負責基礎(chǔ)自動化的一些控制,包括現(xiàn)場執(zhí)行元件的控制,參數(shù)檢測的反饋以及電機的交流傳動控制等,主要采用西門子工業(yè)控制計算機系統(tǒng)和西門子PLC系統(tǒng)實現(xiàn);二級控制負責一些數(shù)據(jù)模型的建立,模型動態(tài)控制,生產(chǎn)計劃編制和流程跟蹤,報表系統(tǒng)等,主要采用工業(yè)以太網(wǎng)實現(xiàn)。
所有電氣和儀表設(shè)備安裝在單獨控制柜里,信號連接到過程控制單元的I/O模塊。通過安裝在PLC繼電器輸出端或輔助繼電器控制所有電磁閥和電機控制。要求的I/O數(shù)量是由驅(qū)動、儀表和其他用電數(shù)量所確定。因此由程序結(jié)構(gòu)確定I/O數(shù)量,并考慮所有要求的驅(qū)動和控制功能包括20%的備用能力。為了內(nèi)存要提供30%的備用能力。每機架至少預(yù)留一個空槽。除了順序控制和聯(lián)鎖外,所有重要任務(wù)如監(jiān)視、管理、過程值控制將在基礎(chǔ)自動化系統(tǒng)(1級)CPU里實現(xiàn)。
RH基礎(chǔ)級控制系統(tǒng)主要用來對煉鋼過程進行實時的監(jiān)測與控制。實現(xiàn)了采集現(xiàn)場信號、進行數(shù)據(jù)處理、邏輯判斷以及現(xiàn)場設(shè)備控制的功能。PLC中的控制軟件是采用西門子提供的Step7V5.4編程工具實現(xiàn)的。畫面監(jiān)控軟件采用WinCC6.2,為實現(xiàn)對監(jiān)視和控制生產(chǎn)過程以及對生產(chǎn)數(shù)據(jù)進行歸檔和進一步處理提供了良好的HMI。
4.1 環(huán)流氣體流量調(diào)節(jié)的PID控制
環(huán)流氣體流量PID調(diào)節(jié)的難點在于如何使得操作人員設(shè)定的環(huán)流氣體總的流量,通過PID程序控制分布到4個支管上各自的調(diào)節(jié)閥進行流量調(diào)節(jié),同時將輸出結(jié)果反饋給調(diào)節(jié)閥進行控制。經(jīng)過仔細研究,在實際生產(chǎn)過程中我們采用了PID串級調(diào)節(jié)的方法。PID調(diào)節(jié)主要包括3個主要參數(shù):設(shè)定值SV、反饋值PV和輸出值MV,把SV與PV進行比較得到MV的值。把操作人員設(shè)定的環(huán)流氣體總的流量除以4后,平均分配到4個支路上的PID控制器的SV值。4個支路上采集到的流量計的過程值作為PV值,各自PID調(diào)節(jié)的輸出結(jié)果為MV值控制各自的調(diào)節(jié)閥。但是在實際的生產(chǎn)過程中我們發(fā)現(xiàn),偶爾出現(xiàn)個別管路堵塞的情況時,真空槽環(huán)流氣體的總量與設(shè)定值差別很大,環(huán)流效果非常差。在控制上做了一些改進,主控制器為我們虛設(shè)的一個控制器,它不直接對現(xiàn)場設(shè)備進行控制,操作人員設(shè)定的環(huán)流氣體總的流量為主控制器的SV值,把4個支路上采集的流量變送器的氣體流量之和為主控制器的PV值,這樣這兩個值進行比較得出主管路上的MV值。把這個MV值除以4后作為4個分支路上PID控制器的SV值,與本分支路上的流量變送器反饋值做比較進行PID調(diào)節(jié)控制本分支路上的流量調(diào)節(jié)閥。
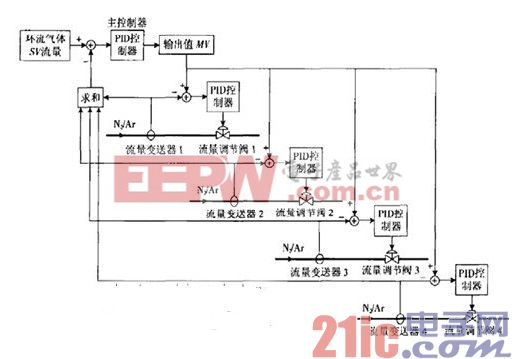
圖4 RH環(huán)流調(diào)節(jié)控制回路
5 系統(tǒng)測試及應(yīng)用
L1子系統(tǒng)有2套西門子PLC控制站,2臺HMI服務(wù)器,2套三電可共用的客戶機,服務(wù)器及客戶機安裝WinCC監(jiān)控軟件,用于現(xiàn)場設(shè)備的控制及狀態(tài)監(jiān)控等。1套L1軟件開發(fā)和系統(tǒng)維護用的工程師站,工程師站安裝Step7編程軟件,2臺L1用報警報表和編程維護打印機,控制站的主站與分站之間通過PROFIBUS網(wǎng)絡(luò)通訊,控制站與服務(wù)器之間和服務(wù)器與客戶機之間通過以太網(wǎng)通訊。
(1)系統(tǒng)軟件測試
由于服務(wù)器、客戶機及工程師站均采用WindowsXP操作系統(tǒng),且服務(wù)器和客戶機安裝有WinCC監(jiān)控軟件,工程師站安裝有Step7編程軟件,所以安裝完上述軟件后,分別進入WindowsXP和WinCC、Step7進行各項操作實驗,檢查系統(tǒng)軟件運行是否正常。
(2)通訊功能測試,通過下裝PLC控制程序和觀察監(jiān)控畫面設(shè)備動作及狀態(tài)變化情況判斷上位機與PLC之間的通訊是否正常,通過畫面操作判斷工程師站與上位機之間的通訊是否正常,通過CPU、電源、通訊模板及I/O模板上的指示燈判斷主站與分站之間的通訊是否正常。
(3)數(shù)字量輸出信號測試
利用Step7軟件提供的強制功能,強制各輸出點,觀察模板上對應(yīng)點的指示燈是否亮,如果通過繼電器控制現(xiàn)場設(shè)備,觀察繼電器是否吸合,還要與現(xiàn)場人員聯(lián)系,確認設(shè)備動作是否正常,這樣既可測試出數(shù)字量輸出摸板上各輸出點輸出是否正常,還能檢查出現(xiàn)場設(shè)備接線是否正常。
6 結(jié)論
本文對新建的RH真空處理的三電自動控制系統(tǒng)的的控制要求、控制理論、控制水平、控制系統(tǒng)的構(gòu)造、控制功能進行了深入的分析和研究。RH真空處理的自動控制系統(tǒng)選型遵循了先進、可靠、實用的原則,節(jié)約投資的原則;設(shè)備選型和裝備水平達到了當前先進的水平。這些工作對于攀鋼以后的新建工程及改造工程的自動控制系統(tǒng)選擇有一定的借鑒意義。
陀螺儀相關(guān)文章:陀螺儀原理
評論