用于電動汽車的功率半導(dǎo)體模塊設(shè)計
成本、可靠性和電子性能及熱性能都會受到封裝的直接影響。但是封裝的另外一個特性也變得越來越重要——即結(jié)構(gòu)因數(shù)。由于OEM推動了功率、效率、可升級性和可靠性要求的提升,因此,成本、重量、尺寸和電感都被要求降低。功率電子集成到電機和制冷設(shè)備中的能力日益提高,這帶來了很大的價值。傳統(tǒng)的電源模塊通常只能為緊湊型機電一體化提供非常有限的范圍,而且確實,如果選擇了這種解決方案,定制化電源模塊將會很快就變得更昂貴,也更加的死板。在這樣的功率水平下,我們認(rèn)為分立式元件難于應(yīng)用,或者真正可用的解決方案根本不能夠處理足夠的功率。最初被棄用的“分立式”方法現(xiàn)在要被主逆變器重新訪問,因為需要電子元件和機機械元件更加緊湊的集成。
本文引用地址:http://m.butianyuan.cn/article/271265.htm目前,在量產(chǎn)中的一種解決方案是采用超級TO-247封裝。搭載一個120A IGBT和二極管的AUIRGPS4067D1器件同時還允許可升級的解決方案,典型地,用來滿足30至80kW范圍主逆變器。與傳統(tǒng)TO-247封裝(如圖3所示)相比,專利型超級TO-247封裝具有一些獨有的特性:首先是采用一個夾子將部件附著在散熱器上,除去了傳統(tǒng)TO-247封裝上出現(xiàn)的螺絲孔,將封裝內(nèi)部的空間最大化,以容納最大可能的芯片。為了與芯片的大電流處理性能相配置,特有的切角引線實現(xiàn)了比傳統(tǒng)TO-247封裝高出30%的橫截面積,從而提高了他們的電流處理性能,并且使得器件運行溫度更低,有更少的寄生電感。切角橫截面同樣可以使器件能安裝到標(biāo)準(zhǔn)TO-247封裝里。封裝上,引腳之間的溝槽增加了爬電距離。最終,符合AEC-Q101的部件要經(jīng)受苛刻的最后測試程序,它包括了正方形RBSOA和100%箝位電感負(fù)載測試。
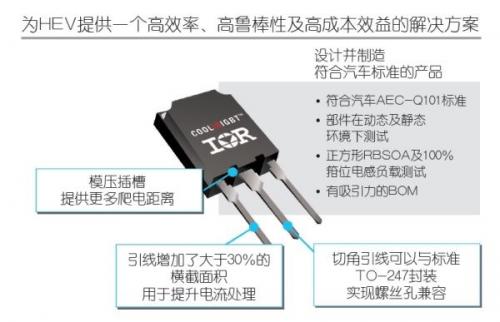
圖3:專利型超級TO-247封裝的優(yōu)勢
簡化廠商成本和柵極驅(qū)動要求的努力不斷推進,客戶希望在其應(yīng)用中降低并聯(lián)的IGBT和二極管的數(shù)量,因此要求大面積芯片的解決方案。由于最新的IGBT和二極管技術(shù)是基于超薄芯片技術(shù),當(dāng)你從超級TO-247這樣的傳統(tǒng)分立式封裝中搬出,構(gòu)建、處理基至是測試這樣的半導(dǎo)體元件就會充滿挑戰(zhàn)。基于這種原因,可以容納大的IGBT和二極管芯片的分立式封裝價值巨大,它們都完全經(jīng)過測試并且易于安裝。CooliRDIE就是正在開發(fā)的解決方案這一。DBC封裝的殼內(nèi)包括一個680V,300A IGBT和一個二極管對,每個芯片都具有可焊接前端金屬表面處理。圖4給出CooliRDIE封裝理念的概覽。
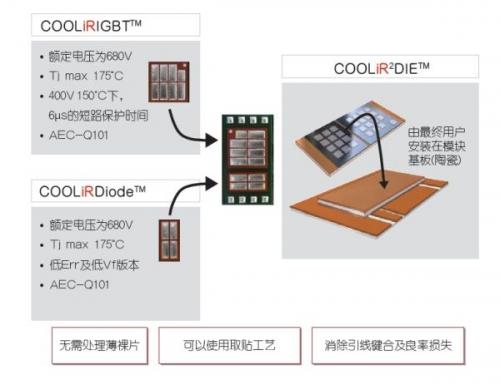
圖4:CooliRDIE封裝
整個無鉛CooliRDIE都是完全的動態(tài)供應(yīng)并經(jīng)過靜態(tài)測試,達(dá)到其卷帶封裝上的額定電流。這就使得客戶能夠采用一處標(biāo)準(zhǔn)的選擇并將機器安置到已經(jīng)準(zhǔn)備好的帶焊盤準(zhǔn)的基座上,處理300A的超薄IGBT和二極管產(chǎn)品。這一部件回流到基底,取代了與大功率模塊相關(guān)的線步驟。省去引線鍵合,提高了可靠性和良率,并且降低了成本、寄生電阻和電感。這些器件可采用兩種版本(正裝和倒裝芯片),可以在一個單獨的基底上形成非常緊湊的半橋布局,無需復(fù)雜的布局模式(如圖5所示)。

圖5:采用CooliRDIE的緊湊型半橋構(gòu)建
事實上,封裝兩端上的電子連接甚至還可以允許封裝用作總線,可以使用一些能夠快速升級的創(chuàng)新型的逆變器布局,如圖6所示。
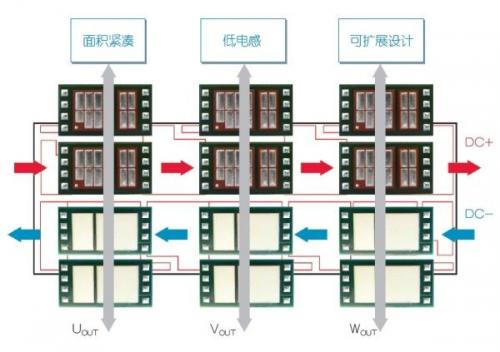
圖6:采用CooliRDIE的可升級逆變器設(shè)計
將可焊接前端金屬增加到硅片上,意味著芯片可以在兩面進行焊接,因此去除了對于焊線的需求。這同樣還有一個優(yōu)點,釋放出了傳統(tǒng)用于焊線的芯片頂部空間——而現(xiàn)在這種空間可用于冷卻。通過從兩面對部件進行制冷的性能,可以將電流處理性能提升50%—或者確實降低相似工作點上的芯片尺寸,并進而降低成本。如果無需雙面制冷,那么僅僅的增加一個頂端的散熱量就可以證明其在提高組裝的散熱性能方面非常有效,進而可以幫助提升短時間峰值電流能力。
評論